గ్రైండింగ్ డిస్క్లు వివిధ పరిశ్రమలలో కీలక పాత్ర పోషిస్తాయి, పదార్థాలను ఆకృతి చేయడం మరియు పూర్తి చేయడం సులభతరం చేస్తాయి. అయితే, ఏదైనా ఇతర సాధనం వలె, వాటి సామర్థ్యం మరియు పనితీరును దెబ్బతీసే సమస్యల నుండి అవి రోగనిరోధక శక్తిని కలిగి ఉండవు. ఈ వ్యాసంలో, మేము సాధారణ గ్రైండింగ్ డిస్క్ సమస్యలను పరిశీలిస్తాము, వాటి మూల కారణాలను అన్వేషిస్తాము మరియు సజావుగా పని చేయడానికి సమర్థవంతమైన పరిష్కారాలను అందిస్తాము.
పరిచయం
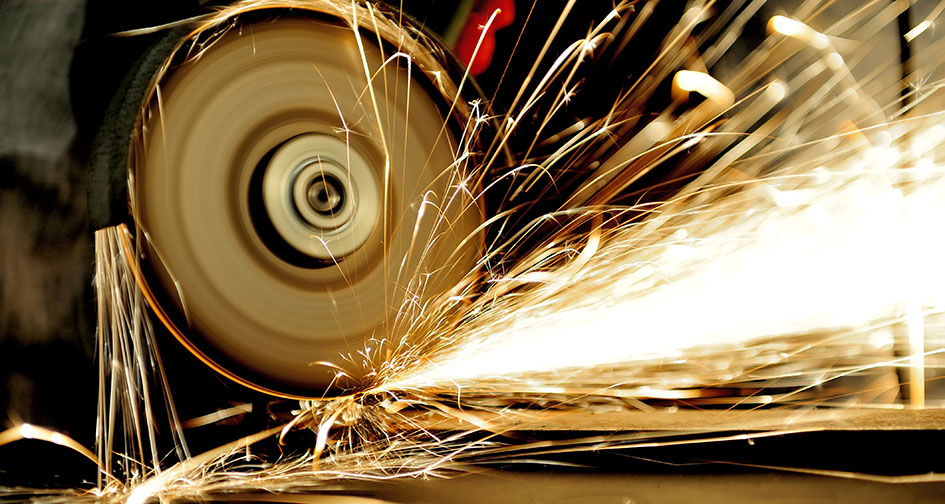
గ్రైండింగ్ డిస్క్లు వివిధ పరిశ్రమలలో ప్రాథమిక పాత్ర పోషిస్తాయి, పదార్థ తొలగింపు, ఆకృతి మరియు ముగింపు ప్రక్రియలకు అవసరమైన సాధనాలుగా పనిచేస్తాయి. వాటి నిర్వచనం, పరిశ్రమలలో ప్రాముఖ్యత మరియు ఎదుర్కొంటున్న సాధారణ సమస్యలను అర్థం చేసుకోవడం వాటి వినియోగాన్ని ఆప్టిమైజ్ చేయడానికి మరియు సమర్థవంతమైన కార్యకలాపాలను నిర్ధారించడానికి చాలా ముఖ్యమైనది.
A. గ్రైండింగ్ డిస్క్ల నిర్వచనం
గ్రైండింగ్ డిస్క్లు అనేవి పదార్థాల ఉపరితలాలను కత్తిరించడానికి, గ్రైండ్ చేయడానికి లేదా పాలిష్ చేయడానికి యంత్ర ప్రక్రియలలో ఉపయోగించే రాపిడి సాధనాలు. ఈ డిస్క్లు సాధారణంగా బ్యాకింగ్ మెటీరియల్కు బంధించబడిన రాపిడి కణాలను కలిగి ఉంటాయి, అదనపు పదార్థాన్ని తొలగించగల, ఉపరితలాలను సున్నితంగా చేయగల లేదా అంచులను పదును పెట్టగల తిరిగే సాధనాన్ని సృష్టిస్తాయి. అవి వివిధ ఆకారాలు మరియు పరిమాణాలలో వస్తాయి, ప్రతి ఒక్కటి నిర్దిష్ట అనువర్తనాల కోసం రూపొందించబడ్డాయి.
బి. వివిధ పరిశ్రమలలో ప్రాముఖ్యత
లోహపు పనిచేసే పరిశ్రమ:
లోహ తయారీ మరియు తయారీలో, లోహ ఉపరితలాలను ఆకృతి చేయడానికి, డీబర్రింగ్ చేయడానికి మరియు పూర్తి చేయడానికి గ్రైండింగ్ డిస్క్లు చాలా ముఖ్యమైనవి. ఖచ్చితమైన కొలతలు మరియు ఉపరితల నాణ్యతను సాధించడానికి వీటిని సాధారణంగా యాంగిల్ గ్రైండర్లతో ఉపయోగిస్తారు.
నిర్మాణ పరిశ్రమ:
నిర్మాణ నిపుణులు కాంక్రీట్ ఉపరితల తయారీ, కఠినమైన అంచులను సున్నితంగా చేయడం మరియు రాయి మరియు కాంక్రీటు వంటి పదార్థాలలో లోపాలను తొలగించడం వంటి పనుల కోసం గ్రైండింగ్ డిస్క్లపై ఆధారపడతారు.
ఆటోమోటివ్ పరిశ్రమ:
ఆటోమోటివ్ రంగంలో పదునుపెట్టే సాధనాల నుండి మెటల్ భాగాలను ఆకృతి చేయడం మరియు పూర్తి చేయడం వరకు గ్రైండింగ్ డిస్క్లు చాలా అవసరం. అవి ఆటోమోటివ్ భాగాల ఖచ్చితత్వం మరియు నాణ్యతకు దోహదం చేస్తాయి.
చెక్క పని పరిశ్రమ:
చెక్క ఉపరితలాలను ఆకృతి చేయడానికి మరియు సున్నితంగా చేయడానికి చెక్క పనివారు గ్రైండింగ్ డిస్క్లను ఉపయోగిస్తారు. ఈ డిస్క్లు అదనపు పదార్థాన్ని తొలగించడంలో, ఆకారాలను మెరుగుపరచడంలో మరియు తదుపరి ముగింపు కోసం కలపను సిద్ధం చేయడంలో ప్రభావవంతంగా ఉంటాయి.
సాధారణ తయారీ:
గ్రైండింగ్ డిస్క్లు వివిధ తయారీ ప్రక్రియలలో అనువర్తనాలను కనుగొంటాయి, ఇక్కడ ఖచ్చితమైన పదార్థ తొలగింపు అవసరం, ఇది అధిక-నాణ్యత భాగాల ఉత్పత్తికి దోహదం చేస్తుంది.
సి. ఎదుర్కొనే సాధారణ సమస్యలు
డిస్క్ వేర్ మరియు అబ్రాషన్:
నిరంతర ఉపయోగం గ్రైండింగ్ డిస్క్ యొక్క అరిగిపోవడానికి మరియు రాపిడికి దారితీస్తుంది, దాని పనితీరును ప్రభావితం చేస్తుంది. సామర్థ్యాన్ని కొనసాగించడానికి క్రమం తప్పకుండా తనిఖీ చేయడం మరియు భర్తీ చేయడం అవసరం.
వేడెక్కడం:
ఎక్కువసేపు వాడటం వలన అధిక ఘర్షణ డిస్క్ వేడెక్కడానికి దారితీస్తుంది, ఇది డిస్క్ యొక్క మన్నిక మరియు పూర్తయిన ఉపరితలం యొక్క నాణ్యతను ప్రభావితం చేస్తుంది. సరైన శీతలీకరణ చర్యలు మరియు ఆవర్తన విరామాలు అవసరం.
అడ్డుపడటం:
గ్రైండింగ్ డిస్క్లు పదార్థ అవశేషాలను కూడబెట్టుకుంటాయి, వాటి ప్రభావాన్ని తగ్గిస్తాయి. క్రమం తప్పకుండా శుభ్రపరచడం లేదా యాంటీ-క్లాగింగ్ లక్షణాలతో డిస్క్లను ఎంచుకోవడం వల్ల ఈ సమస్యను నివారించవచ్చు.
కంపనం మరియు వణుకు:
అసమతుల్యత లేదా అసమాన దుస్తులు కంపనం లేదా చలనానికి దారితీయవచ్చు, ఇది ముగింపు నాణ్యత మరియు ఆపరేషన్ భద్రత రెండింటినీ ప్రభావితం చేస్తుంది. సరైన సంస్థాపన మరియు బ్యాలెన్సింగ్ చాలా కీలకం.
తప్పు డిస్క్ ఎంపిక:
ఒక నిర్దిష్ట పదార్థం లేదా అప్లికేషన్ కోసం తప్పు రకం గ్రైండింగ్ డిస్క్ను ఎంచుకోవడం వలన అసమర్థత మరియు సంభావ్య నష్టం సంభవించవచ్చు. పదార్థ అనుకూలత ఆధారంగా సరైన ఎంపిక అవసరం.
గ్రైండింగ్ డిస్క్లతో సంబంధం ఉన్న నిర్వచనం, ప్రాముఖ్యత మరియు సంభావ్య సవాళ్లను అర్థం చేసుకోవడం ఈ సాధనాలపై ఆధారపడే పరిశ్రమలకు చాలా అవసరం. సాధారణ సమస్యలను పరిష్కరించడం ద్వారా మరియు సరైన వినియోగాన్ని నిర్ధారించడం ద్వారా, పరిశ్రమలు వాటి సంబంధిత అప్లికేషన్లలో గ్రైండింగ్ డిస్క్ల ప్రభావాన్ని పెంచుకోవచ్చు.
గ్రైండింగ్ డిస్క్లపై ధరించడం మరియు చిరిగిపోవడం
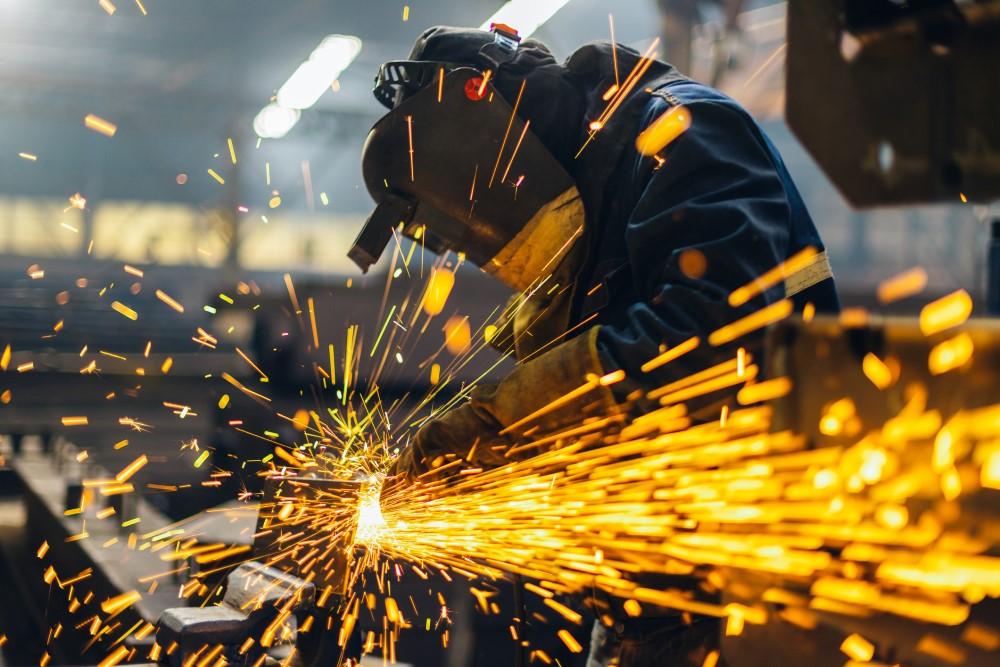
గ్రైండింగ్ డిస్క్లు వివిధ పరిశ్రమలలో అవసరమైన సాధనాలు, ఇవి మెటల్ తయారీ నుండి కాంక్రీట్ పాలిషింగ్ వరకు పనులకు అవసరమైన రాపిడిని అందిస్తాయి. గ్రైండింగ్ డిస్క్లు అరిగిపోవడానికి దోహదపడే అంశాలను అర్థం చేసుకోవడం వాటి పనితీరును ఆప్టిమైజ్ చేయడానికి మరియు భద్రతను నిర్ధారించడానికి చాలా ముఖ్యమైనది.
పదార్థ కాఠిన్యం మరియు కూర్పు:
కాఠిన్యం వైవిధ్యం:గ్రైండింగ్ డిస్క్లు వివిధ కాఠిన్యం స్థాయిలతో కూడిన పదార్థాలను ఎదుర్కొంటాయి. లోహం మరియు కాంక్రీటు వంటి రాపిడి పదార్థాలు కాఠిన్యంలో గణనీయంగా తేడా ఉండవచ్చు. గట్టి పదార్థాలకు వ్యతిరేకంగా నిరంతరం గ్రైండింగ్ చేయడం వల్ల దుస్తులు ధరించడం వేగవంతం అవుతుంది.
పదార్థ కూర్పు:గ్రౌండింగ్ చేస్తున్న పదార్థంలో రాపిడి మూలకాలు ఉండటం గ్రైండింగ్ డిస్క్ యొక్క అరుగుదలపై ప్రభావం చూపుతుంది. రాపిడి కణాలు డిస్క్ అరిగిపోవడాన్ని వేగవంతం చేస్తాయి.
గ్రైండింగ్ ఒత్తిడి మరియు శక్తి:
అధిక ఒత్తిడి:గ్రైండింగ్ డిస్క్ పై అధిక ఒత్తిడిని వర్తింపజేయడం వల్ల త్వరగా అరిగిపోవచ్చు. డిస్క్ పై అనవసరమైన ఒత్తిడిని నివారించడానికి నిర్దిష్ట అప్లికేషన్ కోసం సిఫార్సు చేయబడిన ఒత్తిడిని ఉపయోగించడం చాలా అవసరం.
సరిపోని బలం: మరోవైపు, తగినంత బలం లేకపోవడం వల్ల ఎక్కువసేపు గ్రైండింగ్ జరగవచ్చు, అదనపు ఘర్షణ మరియు వేడిని ఉత్పత్తి చేసి, అరిగిపోవడానికి దోహదం చేస్తుంది.
డిస్క్ నాణ్యత మరియు కూర్పు:
రాపిడి పదార్థం యొక్క నాణ్యత:గ్రైండింగ్ డిస్క్లో ఉపయోగించే రాపిడి పదార్థం యొక్క నాణ్యత దాని జీవితకాలాన్ని గణనీయంగా ప్రభావితం చేస్తుంది. అధిక-నాణ్యత గల రాపిడి పదార్థాలు దుస్తులు ధరించకుండా నిరోధించి, ఎక్కువ కాలం పదునుగా ఉంటాయి.
బాండింగ్ ఏజెంట్:రాపిడి కణాలను కలిపి ఉంచే బాండింగ్ ఏజెంట్ కీలక పాత్ర పోషిస్తుంది. బాగా రూపొందించబడిన బాండింగ్ ఏజెంట్ డిస్క్ యొక్క మన్నికను పెంచుతుంది.
పని వాతావరణ పరిస్థితులు:
ఉష్ణోగ్రత:గ్రైండింగ్ సమయంలో ఉత్పన్నమయ్యే అధిక ఉష్ణోగ్రతలు డిస్క్ యొక్క కూర్పుపై ప్రభావం చూపుతాయి. అధిక వేడి బంధన ఏజెంట్ను బలహీనపరుస్తుంది మరియు దుస్తులు ధరించడాన్ని వేగవంతం చేస్తుంది.
తేమ మరియు కలుషితాలు:పని వాతావరణంలో తేమ లేదా కలుషితాలకు గురికావడం వల్ల గ్రైండింగ్ డిస్క్ యొక్క సమగ్రతపై ప్రభావం చూపుతుంది, దీని వలన అది వేగంగా అరిగిపోతుంది.
ఆపరేటర్ టెక్నిక్:
సరైన సాంకేతికత:ఆపరేటర్ నైపుణ్యం మరియు సాంకేతికత చాలా ముఖ్యమైనవి. సరికాని కోణాల్లో గ్రైండింగ్ చేయడం లేదా అధిక బలాన్ని ఉపయోగించడం వంటి సరికాని ఉపయోగం అసమాన అరిగిపోవడానికి దోహదం చేస్తుంది మరియు డిస్క్ దీర్ఘాయువును తగ్గిస్తుంది.
క్రమం తప్పకుండా తనిఖీలు:ఆపరేటర్లు గ్రైండింగ్ డిస్క్లో ఏవైనా నష్టం లేదా అరిగిపోయిన సంకేతాలు ఉన్నాయా అని క్రమం తప్పకుండా తనిఖీ చేయాలి. ఒక నిర్దిష్ట బిందువుకు మించి అరిగిపోయిన డిస్క్లను వెంటనే భర్తీ చేయాలి.
డిస్క్ పరిమాణం మరియు RPM అనుకూలత:
సరైన పరిమాణం:గ్రైండర్ కోసం సరైన డిస్క్ సైజును ఉపయోగించడం చాలా ముఖ్యం. తప్పు పరిమాణంలో ఉన్న డిస్క్లు అసమానంగా అరిగిపోవచ్చు లేదా భద్రతా ప్రమాదాలను కలిగిస్తాయి.
RPM అనుకూలత:గ్రైండింగ్ డిస్క్ కోసం సిఫార్సు చేయబడిన రివల్యూషన్స్ పర్ మినిట్ (RPM) కు కట్టుబడి ఉండటం వలన సరైన పనితీరు లభిస్తుంది మరియు అకాల దుస్తులు రాకుండా నిరోధించవచ్చు.
క్రమం తప్పకుండా నిర్వహణ, సిఫార్సు చేయబడిన ఆపరేటింగ్ పరిస్థితులకు కట్టుబడి ఉండటం మరియు పనికి సరైన గ్రైండింగ్ డిస్క్ను ఎంచుకోవడం అనేవి అరుగుదల మరియు చిరిగిపోవడాన్ని తగ్గించడానికి అవసరమైన పద్ధతులు. అరుగుదలని ప్రభావితం చేసే అంశాలను అర్థం చేసుకోవడం ద్వారా, ఆపరేటర్లు గ్రైండింగ్ డిస్క్ల దీర్ఘాయువు మరియు సామర్థ్యాన్ని పెంచుకోవచ్చు, సురక్షితమైన మరియు మరింత ఉత్పాదకమైన గ్రైండింగ్ కార్యకలాపాలకు దోహదం చేయవచ్చు.
అసమాన గ్రైండింగ్
అసమాన గ్రైండింగ్ అంటే నేల ఉపరితలం స్థిరమైన మరియు మృదువైన ముగింపును సాధించలేని పరిస్థితిని సూచిస్తుంది. ఈ సమస్య వివిధ కారణాల వల్ల తలెత్తవచ్చు మరియు వర్క్పీస్ నాణ్యతను ప్రభావితం చేయవచ్చు. అసమాన గ్రైండింగ్కు దోహదపడే సాధారణ అంశాలు మరియు సంభావ్య పరిష్కారాలు ఇక్కడ ఉన్నాయి:
తప్పు గ్రైండింగ్ వీల్ ఎంపిక:
పరిష్కారం:గ్రైండింగ్ వీల్ గ్రౌండింగ్ చేయబడిన పదార్థానికి అనుకూలంగా ఉందని నిర్ధారించుకోండి. వివిధ పదార్థాలకు నిర్దిష్ట రాపిడి లక్షణాలు అవసరం. అప్లికేషన్ కోసం సరైన వీల్ రకం, గ్రిట్ పరిమాణం మరియు బాండ్ను ఎంచుకోండి.
సరికాని వీల్ డ్రెస్సింగ్:
కారణం:సరిగ్గా ధరించని గ్రైండింగ్ వీల్ అసమానంగా అరిగిపోవడానికి మరియు అసమర్థమైన కోతకు దారితీస్తుంది.
పరిష్కారం:గ్రైండింగ్ వీల్ ఆకారాన్ని నిలుపుకోవడానికి మరియు పేరుకుపోయిన చెత్తను తొలగించడానికి క్రమం తప్పకుండా డ్రెస్సింగ్ చేయండి. సరైన డ్రెస్సింగ్ స్థిరమైన కట్టింగ్ ఉపరితలాన్ని నిర్ధారిస్తుంది.
గ్రైండింగ్ ఫ్లూయిడ్ లేదా కూలెంట్ సరిపోకపోవడం:
కారణం:గ్రైండింగ్ ద్రవాన్ని తగినంతగా లేదా సరిగ్గా ఉపయోగించకపోవడం వల్ల ఘర్షణ మరియు వేడి పెరుగుతుంది, ఇది అసమాన గ్రైండింగ్కు దారితీస్తుంది.
పరిష్కారం:వేడిని వెదజల్లడానికి మరియు ఘర్షణను తగ్గించడానికి తగిన గ్రైండింగ్ ఫ్లూయిడ్ లేదా కూలెంట్ ఉపయోగించండి. ఏకరీతి ఫలితాలను సాధించడానికి సరైన శీతలీకరణ అవసరం.
తప్పు గ్రైండింగ్ పారామితులు:
కారణం:అధిక వేగం, ఫీడ్ రేటు లేదా కట్ యొక్క లోతు వంటి తప్పు గ్రైండింగ్ పారామితులను ఉపయోగించడం అసమాన గ్రైండింగ్కు దారితీస్తుంది.
పరిష్కారం:పదార్థం మరియు అప్లికేషన్ అవసరాలకు అనుగుణంగా గ్రైండింగ్ పారామితులను సర్దుబాటు చేయండి. సరైన సెట్టింగ్ల కోసం తయారీదారు సిఫార్సులను చూడండి.
అరిగిపోయిన గ్రైండింగ్ వీల్:
కారణం:అరిగిపోయిన గ్రైండింగ్ వీల్ స్థిరమైన కట్టింగ్ ఉపరితలాన్ని అందించకపోవచ్చు, ఫలితంగా అసమాన గ్రైండింగ్ జరుగుతుంది.
పరిష్కారం:గ్రైండింగ్ వీల్ దాని ఉపయోగకరమైన జీవితకాలం ముగిసిన తర్వాత దాన్ని మార్చండి. అరిగిపోయిన సంకేతాల కోసం క్రమం తప్పకుండా వీల్ను తనిఖీ చేయండి.
అసమాన ఒత్తిడి లేదా ఫీడ్ రేటు:
కారణం:గ్రైండింగ్ సమయంలో అసమాన ఒత్తిడి లేదా అస్థిరమైన ఫీడ్ రేట్లు సక్రమంగా పదార్థ తొలగింపుకు దారితీయవచ్చు.
పరిష్కారం:వర్క్పీస్ అంతటా ఏకరీతి ఒత్తిడిని వర్తింపజేయండి మరియు స్థిరమైన ఫీడ్ రేటును నిర్వహించండి. ఆపరేటర్ నైపుణ్యం మరియు వివరాలకు శ్రద్ధ చాలా ముఖ్యం.
యంత్ర సమస్యలు:
కారణం:గ్రైండింగ్ మెషిన్లోని యాంత్రిక సమస్యలు, తప్పుగా అమర్చడం లేదా కుదురుతో సమస్యలు వంటివి అసమానంగా గ్రైండింగ్కు దారితీయవచ్చు.
పరిష్కారం:గ్రైండింగ్ మెషిన్లో క్రమం తప్పకుండా నిర్వహణ తనిఖీలు నిర్వహించండి. సరైన కార్యాచరణను నిర్ధారించుకోవడానికి ఏవైనా యాంత్రిక సమస్యలను వెంటనే పరిష్కరించండి.
వర్క్పీస్ ఫిక్చరింగ్:
కారణం:పేలవంగా భద్రపరచబడిన లేదా తప్పుగా అమర్చబడిన వర్క్పీస్లు అసమాన గ్రైండింగ్కు దారితీయవచ్చు.
పరిష్కారం:వర్క్పీస్ యొక్క సరైన ఫిక్చరింగ్ మరియు అలైన్మెంట్ను నిర్ధారించుకోండి. గ్రైండింగ్ ప్రక్రియలో కదలికను నిరోధించడానికి దానిని గట్టిగా భద్రపరచండి.
అసమాన గ్రైండింగ్ను పరిష్కరించడానికి సరైన పరికరాల సెటప్, సరైన ఆపరేటింగ్ పారామితులు మరియు సాధారణ నిర్వహణ పద్ధతుల కలయిక అవసరం. గ్రైండింగ్ అప్లికేషన్లలో అధిక-నాణ్యత మరియు స్థిరమైన ఫలితాలను సాధించడానికి ఆపరేటర్లకు సమస్యలను గుర్తించి వెంటనే సరిదిద్దడానికి శిక్షణ ఇవ్వాలి. క్రమం తప్పకుండా తనిఖీలు మరియు ఉత్తమ పద్ధతులకు కట్టుబడి ఉండటం గ్రైండింగ్ ప్రక్రియలో సమర్థవంతమైన మరియు ఏకరీతి పదార్థ తొలగింపుకు దోహదం చేస్తుంది.
వేడెక్కడం సమస్యలు
గ్రైండింగ్ సమయంలో వేడెక్కడం అనేది గ్రైండింగ్ వీల్ మరియు వర్క్పీస్ రెండింటి పనితీరును ప్రభావితం చేసే ఒక సాధారణ సమస్య. అధిక వేడి వల్ల వీల్ లైఫ్ తగ్గడం, వర్క్పీస్కు ఉష్ణ నష్టం మరియు మొత్తంగా గ్రైండింగ్ సామర్థ్యం తగ్గడం వంటి వివిధ సమస్యలు తలెత్తుతాయి. ఓవర్హీటింగ్ సమస్యలను పరిష్కరించడానికి సంభావ్య కారణాలు మరియు పరిష్కారాలు ఇక్కడ ఉన్నాయి:
తప్పు గ్రైండింగ్ పారామితులు:
కారణం:అధిక వేగం, ఫీడ్ రేటు లేదా కట్ యొక్క లోతు వంటి సరికాని గ్రైండింగ్ పారామితులను ఉపయోగించడం వలన అదనపు వేడి ఉత్పత్తి అవుతుంది.
పరిష్కారం:సిఫార్సు చేయబడిన పరిధిలో గ్రైండింగ్ పారామితులను సర్దుబాటు చేయండి. గ్రౌండింగ్ చేయబడిన పదార్థం ఆధారంగా సరైన సెట్టింగ్ల కోసం తయారీదారు మార్గదర్శకాలను సంప్రదించండి.
సరిపోని శీతలీకరణ లేదా సరళత:
కారణం:కూలెంట్ లేదా గ్రైండింగ్ ఫ్లూయిడ్ తగినంతగా వాడకపోవడం వల్ల ఘర్షణ మరియు వేడి పెరుగుతుంది.
పరిష్కారం:గ్రైండింగ్ ప్రక్రియలో కూలెంట్ లేదా లూబ్రికెంట్ తగినంత సరఫరా ఉండేలా చూసుకోండి. సరైన శీతలీకరణ వేడిని వెదజల్లడానికి సహాయపడుతుంది మరియు ఉష్ణ నష్టాన్ని నివారిస్తుంది.
తప్పు చక్రాల ఎంపిక:
కారణం:గ్రౌండింగ్ చేస్తున్న పదార్థానికి అనుచితమైన స్పెసిఫికేషన్లతో గ్రైండింగ్ వీల్ను ఎంచుకోవడం వల్ల వేడెక్కడం జరుగుతుంది.
పరిష్కారం:నిర్దిష్ట అప్లికేషన్ కోసం సరైన అబ్రాసివ్ రకం, గ్రిట్ పరిమాణం మరియు బాండ్తో గ్రైండింగ్ వీల్ను ఎంచుకోండి. మెటీరియల్కు వీల్ను సరిపోల్చడం వల్ల వేడి ఉత్పత్తి తగ్గుతుంది.
వర్క్పీస్ మెటీరియల్ సమస్యలు:
కారణం:కొన్ని పదార్థాలు, ముఖ్యంగా తక్కువ ఉష్ణ వాహకత కలిగినవి, గ్రైండింగ్ సమయంలో వేడెక్కే అవకాశం ఎక్కువగా ఉంటుంది.
పరిష్కారం:తక్కువ ఉష్ణ వాహకత కలిగిన పదార్థాల కోసం గ్రైండింగ్ పారామితులను సర్దుబాటు చేయండి. వేడి-సున్నితమైన పదార్థాల కోసం రూపొందించిన ప్రత్యేక గ్రైండింగ్ వీల్ను ఉపయోగించడాన్ని పరిగణించండి.
వీల్ డ్రెస్సింగ్ సమస్యలు:
కారణం:గ్రైండింగ్ వీల్ యొక్క అసమానతలు లేదా సరికాని డ్రెస్సింగ్ అసమాన సంపర్కానికి మరియు వేడి పెరుగుదలకు దారితీస్తుంది.
పరిష్కారం:గ్రైండింగ్ వీల్ ఆకారాన్ని నిలుపుకునేలా మరియు ఏదైనా గ్లేజింగ్ లేదా పేరుకుపోయిన చెత్తను తొలగించేలా క్రమం తప్పకుండా డ్రెస్సింగ్ చేయండి. సరిగ్గా డ్రెస్సింగ్ చేయబడిన చక్రాలు స్థిరమైన గ్రైండింగ్ పనితీరును నిర్ధారిస్తాయి.
సరిపోని యంత్ర నిర్వహణ:
కారణం:సరిగా నిర్వహించని గ్రైండింగ్ యంత్రాలు వేడెక్కడం సమస్యలకు దోహదం చేస్తాయి.
పరిష్కారం:గ్రైండింగ్ మెషీన్ను క్రమం తప్పకుండా నిర్వహించడం, కూలెంట్ సిస్టమ్లను తనిఖీ చేయడం, వీల్ డ్రెస్సింగ్ పరికరాలను తనిఖీ చేయడం మరియు సరైన అమరికను నిర్ధారించడం వంటివి చేయండి. ఏవైనా యాంత్రిక సమస్యలను వెంటనే పరిష్కరించండి.
వీల్ కూలెంట్ ప్రవాహం సరిపోదు:
కారణం:గ్రైండింగ్ జోన్కు తగినంత శీతలకరణి ప్రవాహం లేకపోవడం వల్ల వేడి వెదజల్లడం తగ్గుతుంది.
పరిష్కారం:కూలెంట్ డెలివరీ సిస్టమ్ను తనిఖీ చేసి ఆప్టిమైజ్ చేయండి. కూలింగ్ సామర్థ్యాన్ని నిర్వహించడానికి కూలెంట్ గ్రైండింగ్ జోన్కు సమర్థవంతంగా చేరుకుంటుందని నిర్ధారించుకోండి.
అధిక గ్రైండింగ్ సమయం:
కారణం:విరామం లేకుండా ఎక్కువసేపు గ్రైండింగ్ సెషన్లు వేడి పెరుగుదలకు దోహదం చేస్తాయి.
పరిష్కారం:అధిక వేడి పేరుకుపోకుండా నిరోధించడానికి అడపాదడపా గ్రైండింగ్ను అమలు చేయండి మరియు విరామాలను అనుమతించండి. ఈ విధానం పెద్ద లేదా సవాలుతో కూడిన గ్రైండింగ్ పనులకు చాలా ముఖ్యమైనది.
గ్రైండింగ్లో వేడెక్కడం సమస్యలను పరిష్కరించడానికి సరైన పరికరాల సెటప్, తగిన గ్రైండింగ్ పారామితులు మరియు సాధారణ నిర్వహణ పద్ధతులతో కూడిన సమగ్ర విధానం అవసరం. సరైన పనితీరు, పొడిగించిన సాధన జీవితకాలం మరియు అధిక-నాణ్యత ఫలితాలను నిర్ధారించడానికి ఆపరేటర్లు గ్రైండింగ్ ప్రక్రియలో వేడి ఉత్పత్తిని పర్యవేక్షించాలి మరియు నియంత్రించాలి.
వైబ్రేషన్ ఆందోళనలు
గ్రైండింగ్ ఆపరేషన్ల సమయంలో అధిక కంపనం వివిధ సమస్యలకు దారితీస్తుంది, వీటిలో ఉపరితల నాణ్యత తగ్గడం, సాధనం ధరించడం పెరగడం మరియు గ్రైండింగ్ యంత్రానికి సంభావ్య నష్టం జరగవచ్చు. ఖచ్చితమైన మరియు సమర్థవంతమైన గ్రైండింగ్ ప్రక్రియలను సాధించడానికి కంపన సమస్యలను పరిష్కరించడం చాలా ముఖ్యం. కంపన సమస్యలను తగ్గించడానికి సంభావ్య కారణాలు మరియు పరిష్కారాలు ఇక్కడ ఉన్నాయి:
అసమాన చక్రాల దుస్తులు:
కారణం:గ్రైండింగ్ వీల్ సక్రమంగా అరిగిపోవడం వల్ల వర్క్పీస్తో అసమాన సంబంధం ఏర్పడి, కంపనాలకు కారణమవుతుంది.
పరిష్కారం:స్థిరమైన మరియు చదునైన ఉపరితలాన్ని నిర్వహించడానికి గ్రైండింగ్ వీల్ను క్రమం తప్పకుండా తనిఖీ చేసి డ్రెస్సింగ్ చేయండి. సరైన చక్రాల నిర్వహణ కంపనాలను తగ్గించడంలో సహాయపడుతుంది.
అసమతుల్య గ్రైండింగ్ వీల్:
కారణం:గ్రైండింగ్ వీల్లో అసమతుల్యత, అది అసమానంగా ధరించడం వల్ల లేదా తయారీ లోపాల వల్ల అయినా, కంపనానికి దారితీస్తుంది.
పరిష్కారం:వీల్ బ్యాలెన్సర్ ఉపయోగించి గ్రైండింగ్ వీల్ను బ్యాలెన్స్ చేయండి. బ్యాలెన్సింగ్ బరువు యొక్క సమాన పంపిణీని నిర్ధారిస్తుంది మరియు ఆపరేషన్ సమయంలో కంపనాలను తగ్గిస్తుంది.
సరిపోని యంత్ర అమరిక:
కారణం:వీల్ స్పిండిల్ లేదా వర్క్టేబుల్ వంటి యంత్ర భాగాల పేలవమైన క్రమాంకనం లేదా తప్పుగా అమర్చడం కంపనాలకు దోహదం చేస్తుంది.
పరిష్కారం:సరైన కార్యాచరణను నిర్ధారించడానికి యంత్ర భాగాలను క్రమం తప్పకుండా క్రమాంకనం చేయండి మరియు సమలేఖనం చేయండి. యంత్ర సెటప్ మరియు అమరిక కోసం తయారీదారు మార్గదర్శకాలను అనుసరించండి.
వర్క్పీస్ అసమతుల్యత:
కారణం:అసమానంగా లేదా సరిగ్గా భద్రపరచబడని వర్క్పీస్ అసమతుల్యతను సృష్టించి, కంపనాలను ప్రేరేపిస్తుంది.
పరిష్కారం:వర్క్పీస్ను సరిగ్గా భద్రపరచండి, అది సమానంగా ఉంచబడి బిగించబడిందని నిర్ధారించుకోండి. గ్రైండింగ్ ప్రక్రియను ప్రారంభించే ముందు ఏవైనా అసమతుల్యత సమస్యలను పరిష్కరించండి.
తప్పు చక్రాల ఎంపిక:
కారణం:తగని స్పెసిఫికేషన్లతో గ్రైండింగ్ వీల్ని ఉపయోగించడం వల్ల కంపనాలు సంభవించవచ్చు.
పరిష్కారం:సరైన అబ్రాసివ్ రకం, గ్రిట్ పరిమాణం మరియు గ్రౌండింగ్ చేయబడిన పదార్థానికి బంధం ఉన్న గ్రైండింగ్ వీల్ను ఎంచుకోండి. అప్లికేషన్కు వీల్ను సరిపోల్చడం వల్ల కంపనాలు తగ్గుతాయి.
మెషిన్ వేర్ అండ్ టయర్:
కారణం:బేరింగ్లు లేదా స్పిండిల్స్ వంటి అరిగిపోయిన లేదా దెబ్బతిన్న యంత్ర భాగాలు కంపనాలకు దోహదం చేస్తాయి.
పరిష్కారం:అరిగిపోయిన యంత్ర భాగాలను క్రమం తప్పకుండా తనిఖీ చేసి భర్తీ చేయండి. సరైన నిర్వహణ అధిక కంపనాలను నివారించడానికి మరియు గ్రైండింగ్ యంత్రం యొక్క జీవితాన్ని పొడిగించడానికి సహాయపడుతుంది.
సరిపోని శీతలకరణి ప్రవాహం:
కారణం:గ్రైండింగ్ జోన్కు తగినంత శీతలకరణి ప్రవాహం లేకపోవడం వల్ల వేడి పేరుకుపోవడం మరియు కంపనాలు ఏర్పడతాయి.
పరిష్కారం:సరైన శీతలీకరణను నిర్ధారించడానికి కూలెంట్ డెలివరీ వ్యవస్థను ఆప్టిమైజ్ చేయండి. ప్రభావవంతమైన శీతలీకరణ ఉష్ణ విస్తరణ మరియు సంకోచ ప్రమాదాన్ని తగ్గిస్తుంది, ఇది కంపనాలకు దారితీస్తుంది.
టూల్ హోల్డర్ సమస్యలు:
కారణం:టూల్ హోల్డర్ లేదా స్పిండిల్ ఇంటర్ఫేస్తో సమస్యలు కంపనాలను కలిగిస్తాయి.
పరిష్కారం:టూల్ హోల్డర్ సురక్షితంగా అమర్చబడి, స్పిండిల్తో సరిగ్గా సమలేఖనం చేయబడిందని నిర్ధారించుకోండి. కంపనాలను తగ్గించడానికి అధిక నాణ్యత గల మరియు సరిగ్గా నిర్వహించబడే టూల్ హోల్డర్లను ఉపయోగించండి.
మెషిన్ ఫౌండేషన్:
కారణం:యంత్ర పునాది సరిగా లేకపోవడం లేదా తగినంత మద్దతు లేకపోవడం కంపనాలను అధికం చేస్తుంది.
పరిష్కారం:గ్రైండింగ్ మెషిన్ స్థిరమైన మరియు సరిగ్గా రూపొందించబడిన పునాదిపై ఇన్స్టాల్ చేయబడిందని నిర్ధారించుకోండి. యంత్రానికి ప్రసరించే కంపనాలను తగ్గించడానికి ఏవైనా నిర్మాణాత్మక సమస్యలను పరిష్కరించండి.
గ్రైండింగ్లో వైబ్రేషన్ సమస్యలను సమర్థవంతంగా పరిష్కరించడానికి సరైన యంత్ర నిర్వహణ, చక్రాల ఎంపిక మరియు వర్క్పీస్ నిర్వహణ కలయిక అవసరం. సమస్యలను గుర్తించి వెంటనే పరిష్కరించడానికి ఆపరేటర్లు క్రమం తప్పకుండా తనిఖీ మరియు నిర్వహణ పద్ధతులను అమలు చేయాలి, ఫలితంగా గ్రైండింగ్ పనితీరు మరియు నాణ్యత మెరుగుపడుతుంది.
గ్రైండింగ్లో లోడింగ్ సమస్యలు
గ్రైండింగ్లో లోడింగ్ అంటే గ్రైండింగ్ వీల్లోని రాపిడి గ్రెయిన్ల మధ్య ఖాళీలు గ్రౌండింగ్ చేయబడిన పదార్థంతో నిండిపోయే దృగ్విషయాన్ని సూచిస్తుంది, ఫలితంగా కటింగ్ చర్య తగ్గుతుంది మరియు ఘర్షణ పెరుగుతుంది. లోడింగ్ గ్రైండింగ్ ప్రక్రియ యొక్క సామర్థ్యం మరియు నాణ్యతను ప్రతికూలంగా ప్రభావితం చేస్తుంది. లోడింగ్ సమస్యలను పరిష్కరించడానికి సంభావ్య కారణాలు మరియు పరిష్కారాలు ఇక్కడ ఉన్నాయి:
సాఫ్ట్ వర్క్పీస్ మెటీరియల్:
కారణం:మృదువైన పదార్థాలను రుబ్బుకోవడం వల్ల రాపిడి ధాన్యాలు వేగంగా మూసుకుపోతాయి.
పరిష్కారం:మృదువైన పదార్థాలపై పనిచేసేటప్పుడు ముతక గ్రిట్ మరియు ఓపెన్ స్ట్రక్చర్ ఉన్న గ్రైండింగ్ వీల్ను ఉపయోగించండి. ఇది త్వరగా లోడ్ అవ్వకుండా నిరోధించడంలో సహాయపడుతుంది మరియు సమర్థవంతమైన చిప్ తొలగింపును అనుమతిస్తుంది.
పదార్థ కాలుష్యం:
కారణం:వర్క్పీస్ మెటీరియల్లో ఉండే కలుషితాలు, నూనెలు, గ్రీజు లేదా శీతలకరణి అవశేషాలు వంటివి లోడింగ్కు దోహదం చేస్తాయి.
పరిష్కారం:కలుషితాలను తొలగించడానికి గ్రైండింగ్ చేసే ముందు వర్క్పీస్ను సరిగ్గా శుభ్రం చేసుకోండి. లోడింగ్ను తగ్గించడానికి తగిన కటింగ్ ద్రవాలు లేదా కూలెంట్లను ఉపయోగించండి.
తప్పుడు కూలెంట్ అప్లికేషన్:
కారణం:కూలెంట్ను సరిపోని లేదా సరికాని అప్లికేషన్ తగినంత లూబ్రికేషన్ మరియు కూలింగ్కు దారితీస్తుంది, ఫలితంగా లోడింగ్ ఏర్పడుతుంది.
పరిష్కారం:కూలెంట్ ప్రవాహాన్ని మరియు ఏకాగ్రతను ఆప్టిమైజ్ చేయండి. కూలెంట్ గ్రైండింగ్ జోన్కు సమర్థవంతంగా చేరుకుని, ప్రక్రియను ద్రవపదార్థం చేసి చల్లబరుస్తుంది, లోడ్ అవ్వకుండా నిరోధిస్తుంది.
తగినంత చక్రాల పదును లేకపోవడం:
కారణం:నిస్తేజంగా లేదా అరిగిపోయిన గ్రైండింగ్ వీల్స్ వాటి కటింగ్ సామర్థ్యాన్ని కోల్పోతాయి కాబట్టి అవి లోడ్ అయ్యే అవకాశం ఎక్కువగా ఉంటుంది.
పరిష్కారం:గ్రైండింగ్ వీల్ పదునుగా ఉంచడానికి క్రమం తప్పకుండా డ్రస్ చేసి పదును పెట్టండి. తాజా రాపిడి ధాన్యాలను బహిర్గతం చేయడానికి మరియు కటింగ్ చర్యను మెరుగుపరచడానికి వీల్ డ్రస్సర్ను ఉపయోగించండి.
తక్కువ చక్రాల వేగం:
కారణం:గ్రైండింగ్ వీల్ను తక్కువ వేగంతో ఆపరేట్ చేయడం వల్ల చిప్లను బయటకు తీయడానికి తగినంత సెంట్రిఫ్యూగల్ ఫోర్స్ లభించకపోవచ్చు, దీని వలన లోడింగ్ ఏర్పడుతుంది.
పరిష్కారం:నిర్దిష్ట చక్రం మరియు వర్క్పీస్ కలయిక కోసం సిఫార్సు చేయబడిన వేగంతో గ్రైండింగ్ మెషిన్ పనిచేస్తుందని నిర్ధారించుకోండి. అధిక వేగం మెరుగైన చిప్ తొలగింపుకు సహాయపడుతుంది.
అధిక ఒత్తిడి:
కారణం:గ్రౌండింగ్ సమయంలో ఎక్కువ ఒత్తిడిని వర్తింపజేయడం వలన పదార్థం చక్రంలోకి బలవంతంగా నెట్టబడుతుంది, దీనివల్ల లోడింగ్ ఏర్పడుతుంది.
పరిష్కారం:మితమైన మరియు స్థిరమైన గ్రైండింగ్ ఒత్తిడిని ఉపయోగించండి. లోడింగ్కు దారితీసే అధిక ఒత్తిడి లేకుండా చక్రం సమర్థవంతంగా కత్తిరించడానికి ఫీడ్ రేటును సర్దుబాటు చేయండి.
తప్పు చక్రాల లక్షణాలు:
కారణం:గ్రౌండింగ్ చేస్తున్న పదార్థానికి సరికాని స్పెసిఫికేషన్లతో గ్రైండింగ్ వీల్ని ఉపయోగించడం వల్ల లోడింగ్ జరగవచ్చు.
పరిష్కారం:నిర్దిష్ట అప్లికేషన్ కోసం తగిన రాపిడి రకం, గ్రిట్ పరిమాణం మరియు బాండ్తో గ్రైండింగ్ వీల్ను ఎంచుకోండి. చక్రాన్ని పదార్థానికి సరిపోల్చడం వల్ల లోడింగ్ను నిరోధించవచ్చు.
సరిపోని శీతలకరణి శుభ్రపరచడం:
కారణం:కలుషితమైన లేదా పాత కూలెంట్ లోడింగ్ సమస్యలకు దోహదం చేస్తుంది.
పరిష్కారం:కలుషితాలు పేరుకుపోకుండా నిరోధించడానికి కూలెంట్ను క్రమం తప్పకుండా శుభ్రం చేసి భర్తీ చేయండి. తాజా మరియు శుభ్రమైన కూలెంట్ లూబ్రికేషన్ మరియు శీతలీకరణను పెంచుతుంది, లోడ్ అయ్యే అవకాశాన్ని తగ్గిస్తుంది.
సరికాని డ్రెస్సింగ్ టెక్నిక్:
కారణం:గ్రైండింగ్ వీల్ యొక్క సరికాని డ్రెస్సింగ్ అసమానతలు మరియు లోడింగ్కు దారితీస్తుంది.
పరిష్కారం:తగిన డ్రెస్సింగ్ సాధనాన్ని ఉపయోగించి వీల్ను సరిగ్గా డ్రెస్ చేయండి. లోడింగ్ను నిరోధించడానికి వీల్ ప్రొఫైల్ స్థిరంగా మరియు అసమానతలు లేకుండా ఉండేలా చూసుకోండి.
లోడింగ్ సమస్యలను సమర్థవంతంగా పరిష్కరించడంలో సరైన చక్రాల ఎంపిక, యంత్ర సెటప్ మరియు నిర్వహణ పద్ధతుల కలయిక ఉంటుంది. ఆపరేటర్లు సిఫార్సు చేసిన విధానాలను అనుసరించాలి, తగిన గ్రైండింగ్ పారామితులను ఉపయోగించాలి మరియు లోడింగ్ను తగ్గించడానికి మరియు గ్రైండింగ్ పనితీరును ఆప్టిమైజ్ చేయడానికి సాధారణ వీల్ డ్రెస్సింగ్ను అమలు చేయాలి.
వివిధ మెటల్ వర్కింగ్ మరియు ఫాబ్రికేషన్ అప్లికేషన్లలో సరైన ఫలితాలను సాధించడానికి సరైన గ్రైండింగ్ డిస్క్ను ఎంచుకోవడం చాలా ముఖ్యం. ఎంపిక పని చేస్తున్న పదార్థం, కావలసిన ముగింపు మరియు ఉపయోగించే గ్రైండర్ రకం వంటి అంశాలపై ఆధారపడి ఉంటుంది.
సరైన గ్రైండింగ్ డిస్క్ను ఎంచుకోవడం
మెటీరియల్ అనుకూలత:
ఫెర్రస్ లోహాలు (ఉక్కు, ఇనుము):ఫెర్రస్ లోహాల కోసం ప్రత్యేకంగా రూపొందించిన గ్రైండింగ్ డిస్క్లను ఉపయోగించండి. ఈ డిస్క్లు తరచుగా ఉక్కు కాఠిన్యానికి తగిన అబ్రాసివ్లను కలిగి ఉంటాయి మరియు లోడ్ అయ్యే అవకాశం తక్కువగా ఉంటుంది.
నాన్-ఫెర్రస్ లోహాలు (అల్యూమినియం, ఇత్తడి):మృదువైన లోహాలకు అనువైన అబ్రాసివ్లు ఉన్న డిస్క్లను ఎంచుకోండి, తద్వారా అవి మూసుకుపోకుండా ఉంటాయి. అల్యూమినియం ఆక్సైడ్ లేదా సిలికాన్ కార్బైడ్ డిస్క్లు సాధారణ ఎంపికలు.
రాపిడి పదార్థం:
అల్యూమినియం ఆక్సైడ్:ఫెర్రస్ లోహాలపై సాధారణ ప్రయోజన గ్రైండింగ్కు అనుకూలం. ఇది మన్నికైనది మరియు బహుముఖమైనది.
జిర్కోనియా అల్యూమినా:అధిక కట్టింగ్ సామర్థ్యం మరియు దీర్ఘాయువును అందిస్తుంది, ఇది ఫెర్రస్ మరియు నాన్-ఫెర్రస్ లోహాలపై దూకుడుగా గ్రైండింగ్ చేయడానికి అనుకూలంగా ఉంటుంది.
సిలికాన్ కార్బైడ్:ఫెర్రస్ కాని లోహాలు మరియు రాళ్లను గ్రైండ్ చేయడానికి అనువైనది. ఇది అల్యూమినియం ఆక్సైడ్ కంటే పదునైనది కానీ తక్కువ మన్నికైనది.
గ్రిట్ సైజు:
కోర్స్ గ్రిట్ (24-36):వేగవంతమైన స్టాక్ తొలగింపు మరియు భారీ-డ్యూటీ గ్రైండింగ్.
మీడియం గ్రిట్ (40-60):స్టాక్ తొలగింపు మరియు ఉపరితల ముగింపును సమతుల్యం చేస్తుంది.
ఫైన్ గ్రిట్ (80-120):ఉపరితల తయారీకి మరియు తేలికగా గ్రైండింగ్ చేయడానికి అనువైన మృదువైన ముగింపును అందిస్తుంది.
చక్రం రకం:
రకం 27 (డిప్రెస్డ్ సెంటర్):చదునైన ఉపరితలంతో కూడిన ప్రామాణిక గ్రైండింగ్ డిస్క్, ఉపరితల గ్రైండింగ్ మరియు అంచు పనికి అనువైనది.
రకం 29 (శంఖాకార):దూకుడుగా స్టాక్ తొలగింపు మరియు మెరుగైన ఉపరితల బ్లెండింగ్ కోసం కోణీయ డిజైన్.
రకం 1 (నేరుగా):కట్-ఆఫ్ అప్లికేషన్లకు ఉపయోగిస్తారు. ఇది ఖచ్చితమైన కటింగ్ కోసం సన్నని ప్రొఫైల్ను అందిస్తుంది.
అప్లికేషన్:
గ్రైండింగ్:పదార్థ తొలగింపు మరియు ఆకృతి కోసం ప్రామాణిక గ్రైండింగ్ డిస్క్లు.
కట్టింగ్:లోహాన్ని కత్తిరించడానికి కట్-ఆఫ్ వీల్స్ ఉపయోగించండి, ఇది నేరుగా మరియు శుభ్రమైన అంచుని అందిస్తుంది.
ఫ్లాప్ డిస్క్లు:గ్రైండింగ్ మరియు ఫినిషింగ్ను ఒకదానిలో కలపండి. ఉపరితలాలను బ్లెండింగ్ మరియు స్మూత్ చేయడానికి అనుకూలం.
గ్రైండర్ తో అనుకూలత:
గ్రైండింగ్ డిస్క్ మీరు ఉపయోగిస్తున్న గ్రైండర్ రకం మరియు వేగానికి అనుకూలంగా ఉందని నిర్ధారించుకోండి. డిస్క్ యొక్క గరిష్ట RPM (నిమిషానికి విప్లవాలు) కోసం తయారీదారు సిఫార్సులను తనిఖీ చేయండి.
పని ప్రత్యేకత:
భారీ స్టాక్ తొలగింపు:సమర్థవంతమైన పదార్థ తొలగింపు కోసం ముతక గ్రిట్ మరియు టైప్ 27 లేదా టైప్ 29 డిస్క్ను ఎంచుకోండి.
ఉపరితల ముగింపు:సున్నితమైన ముగింపుల కోసం ఫ్లాప్ డిస్క్లతో మీడియం నుండి ఫైన్ గ్రిట్లను ఎంచుకోండి.
భద్రతా పరిగణనలు:
భద్రతా మార్గదర్శకాలను అనుసరించండి, వీటిలో భద్రతా గ్లాసెస్ మరియు చేతి తొడుగులు వంటి తగిన వ్యక్తిగత రక్షణ పరికరాలు (PPE) ధరించడం కూడా ఉంటుంది.
అదనపు మన్నిక మరియు భద్రత కోసం రీన్ఫోర్స్డ్ డిస్క్లను ఎంచుకోండి.
బ్రాండ్ మరియు నాణ్యత:
నాణ్యత మరియు స్థిరత్వానికి ప్రసిద్ధి చెందిన ప్రసిద్ధ బ్రాండ్ల నుండి డిస్క్లను ఎంచుకోండి. అధిక-నాణ్యత డిస్క్లు మెరుగైన పనితీరు మరియు మన్నికను అందిస్తాయి.
ఖర్చు పరిగణన:
ప్రారంభ ఖర్చును గ్రైండింగ్ డిస్క్ యొక్క అంచనా జీవితకాలం మరియు పనితీరుతో సమతుల్యం చేయండి. అధిక-నాణ్యత డిస్క్లు ముందస్తు ఖర్చు ఎక్కువగా ఉండవచ్చు కానీ కాలక్రమేణా మెరుగైన విలువను అందించగలవు.
ఈ అంశాలను పరిగణనలోకి తీసుకోవడం ద్వారా, ఆపరేటర్లు వారి నిర్దిష్ట అప్లికేషన్లకు సరైన గ్రైండింగ్ డిస్క్ను ఎంచుకోవచ్చు, సామర్థ్యం, భద్రత మరియు సరైన ఫలితాలను నిర్ధారిస్తారు.
ముగింపు
ముగింపులో, విజయవంతమైన లోహపు పని మరియు తయారీ ఫలితాలను సాధించడంలో తగిన గ్రైండింగ్ డిస్క్ను ఎంచుకోవడం కీలకమైన అంశం. ఎంపిక పని చేస్తున్న పదార్థం, కావలసిన ముగింపు మరియు ఉపయోగంలో ఉన్న గ్రైండర్ రకం వంటి వివిధ అంశాలపై ఆధారపడి ఉంటుంది. మెటీరియల్ అనుకూలత, రాపిడి రకం, గ్రిట్ పరిమాణం, చక్రం రకం, అప్లికేషన్, గ్రైండర్ అనుకూలత, పని నిర్దిష్టత, భద్రత, బ్రాండ్ నాణ్యత మరియు ఖర్చును పరిగణనలోకి తీసుకోవడం ద్వారా, ఆపరేటర్లు తమ గ్రైండింగ్ ప్రక్రియలలో సామర్థ్యం మరియు భద్రతను పెంచడానికి సమాచారంతో కూడిన నిర్ణయాలు తీసుకోవచ్చు.
భద్రతా మార్గదర్శకాలకు కట్టుబడి ఉండటం, తగిన వ్యక్తిగత రక్షణ పరికరాలను ధరించడం మరియు గ్రైండర్ మరియు డిస్క్ అనుకూలత కోసం తయారీదారు సిఫార్సులను అనుసరించడం చాలా అవసరం. ఇది భారీ స్టాక్ తొలగింపు, ఉపరితల ముగింపు లేదా కటింగ్ అప్లికేషన్ల కోసం అయినా, సరైన గ్రైండింగ్ డిస్క్ పని నాణ్యత మరియు సామర్థ్యాన్ని గణనీయంగా ప్రభావితం చేస్తుంది.
అదనంగా, అరిగిపోవడం కోసం కాలానుగుణ తనిఖీలు, వేడెక్కడం మరియు వైబ్రేషన్ సమస్యలు వంటి సమస్యలను పరిష్కరించడం మరియు లోడింగ్ సమస్యలను అర్థం చేసుకోవడం గ్రైండింగ్ డిస్క్ యొక్క జీవితకాలాన్ని పొడిగించడానికి మరియు స్థిరమైన పనితీరును నిర్ధారించడానికి దోహదం చేస్తాయి.
సారాంశంలో, గ్రైండింగ్ డిస్క్లను ఎంచుకోవడం, ఉపయోగించడం మరియు నిర్వహించడం గురించి బాగా తెలిసిన మరియు క్రమబద్ధమైన విధానం సరైన ఫలితాలను సాధించడానికి, ఉత్పాదకతను పెంచడానికి మరియు సురక్షితమైన పని వాతావరణాన్ని నిర్ధారించడానికి కీలకం.
పోస్ట్ సమయం: జనవరి-12-2024